The Day the Docks Went Silent
Tuesday morning, 50,000 dockworkers dropped their tools and walked off the job. Suddenly, East and Gulf Coast seaports—usually bustling with activity—became ghost towns. Cargo ships sat idle, goods piled up, and chaos spread through the supply chain.
It’s easy to forget that our seamless shopping experiences depend on these workers. When even one link in the chain breaks, the fallout is massive: delayed goods, empty shelves, and rising prices. This strike has turned a labor dispute into a logistical nightmare.
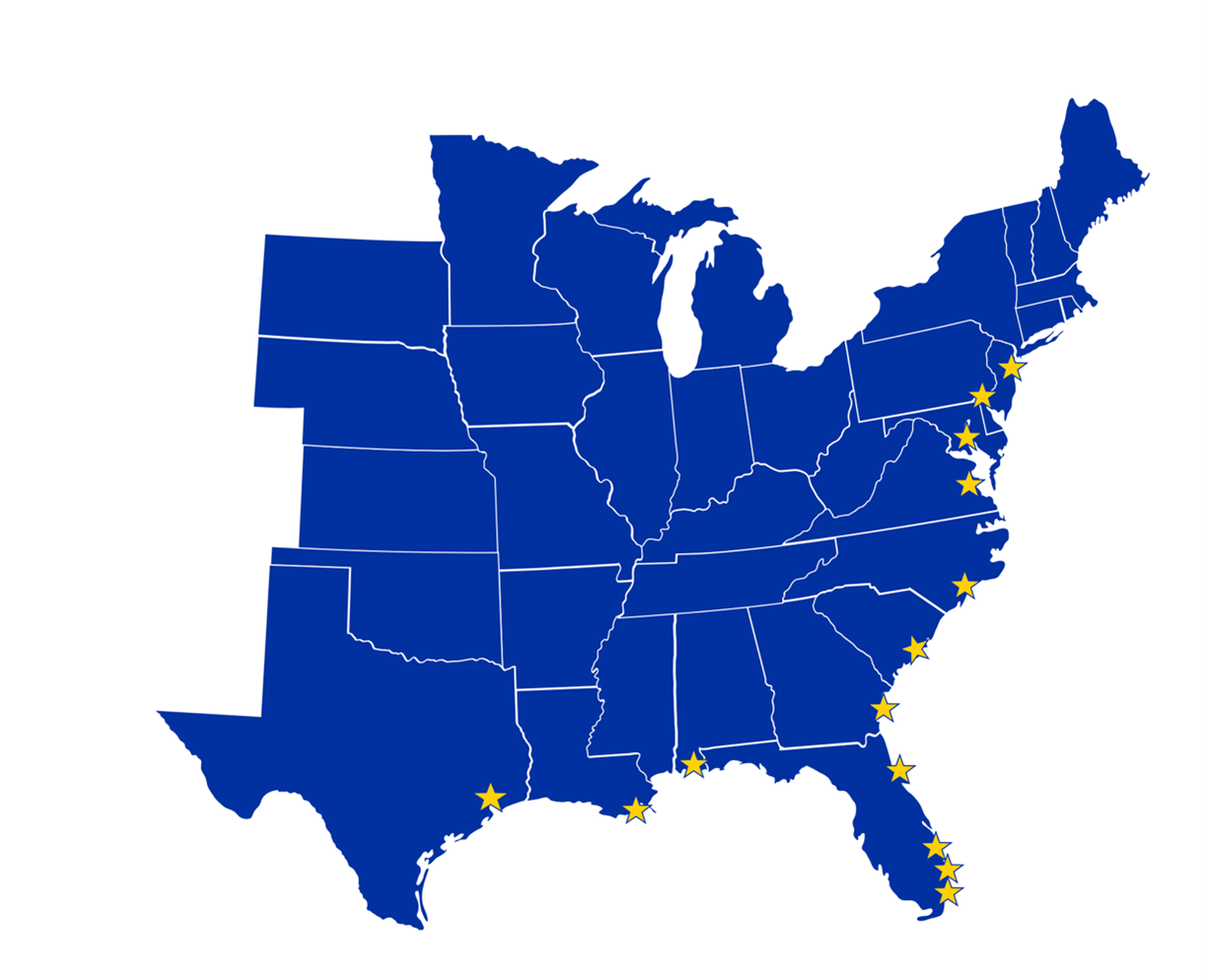
East Coast and Gulf Coast Ports | Source: National Association of Manufacturers
“I Will Cripple You”
It’s a dramatic line that sets the tone for the escalating clash between the International Longshoremen’s Association (ILA) and the United States Maritime Alliance (USMCA). This standoff isn’t just about salaries—it’s a fight against the inevitable march of technology. The ILA has gone on strike, not just for a hefty pay raise but to halt the automation that threatens to transform ports into digital landscapes, potentially sidelining the workforce that’s kept them moving for decades.

ILA President Harold Daggett | Source: International Longshoreman’s Association
The Core of the Conflict: Wages vs. Automation
The ILA’s demands are steep: a 77% raise over six years and a complete ban on port automation. The USMC had already proposed a generous 50% raise, but the ILA saw it as insufficient given what was at stake. Dockworkers argue that port automation directly threatens job security and are unwilling to budge.
The reality is that U.S. port workers are already among the best-paid in blue-collar America. Starting at a base rate of $39 an hour (over $81,000 annually), many make over six figures with overtime. Crane operators and supervisors can earn $200,000 to $500,000 annually, and ILA President Harold Daggett pulls in a cool $900,000 annually. These earnings are substantially higher than the national average salary of $59,428.
So, why the resistance? It’s not just about the paycheck—it’s about power and future-proofing their livelihoods. The ILA knows it has leverage, and it’s using it to prevent an uncertain future in which machines might take over human roles.
The Need for Balance
While the ILA’s concerns are understandable, resisting automation might not be the wisest move. Ports worldwide are adopting technology to streamline operations, and the U.S. needs to catch up. Intelligent automation doesn’t have to mean fewer jobs; it can lead to better, safer positions that require new skills. The challenge is balancing embracing technological progress and ensuring that human workers are included.
Instead of pushing for a blanket ban on automation, the focus should shift to retraining programs, investment in education, and creating hybrid roles that combine human oversight with automated systems. Port workers could transition from manual labor to tech supervisors, ensuring that people and machines work harmoniously.
The Real Cost of Compromise
But if the ILA wins and blocks port automation, who will pay the price? The answer is simple: the consumers. Logistics companies, facing ballooning labor costs, will pass those expenses down the supply chain, leading to higher prices on everyday goods. Inflation will creep up, and that “win” for port workers suddenly looks like a costly loss for everyone else.
While the ILA might win this battle, the broader war could see U.S. ports falling behind global competition, causing long-term economic consequences. It’s a classic case of short-term gain versus long-term pain.
Ports in markets like China tend to look like this:
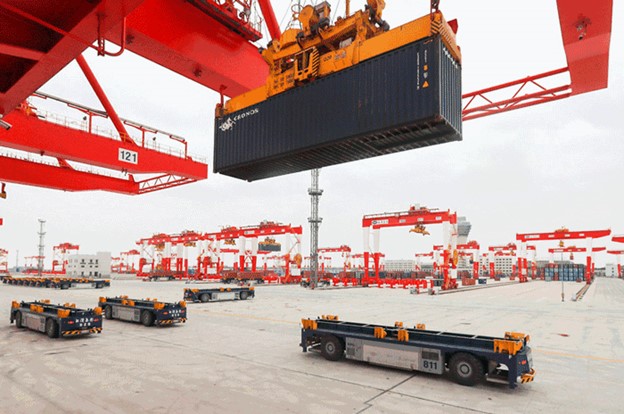
Source: Huawei
Automation: Enemy or Ally?
Rather than viewing automation as an enemy, it’s time to see it as a potential ally. Ports that integrate automation effectively have seen productivity skyrocket. Singapore’s ports, for example, are some of the most advanced in the world, using AI-driven systems to handle cargo with incredible efficiency and speed. These advancements don’t have to come at the cost of human workers, but they require a strategic approach that ensures everyone benefits.
U.S. ports can adopt a hybrid model where human expertise and robotic efficiency combine to create a more productive, safer, and future-proof system. The ILA’s fears, while valid, need to be addressed through dialogue and innovation, not resistance.
The Path Forward
The ILA’s demands might sound extreme, but they underscore a fundamental question that industries everywhere are grappling with: How do we integrate technology without sidelining the people who’ve built these industries? The answer lies in collaboration and compromise, not confrontation.
If U.S. ports can find a way to modernize without sacrificing jobs, they could set a powerful example for other industries facing the same challenges. It’s not about halting progress; it’s about harnessing it for the benefit of all.
In the end, the phrase “I will cripple you” shouldn’t be the union’s stance against automation. Instead, it should serve as a rallying cry for finding a new way forward—one where technology and human ingenuity work hand-in-hand to build a stronger, more competitive future.